ビジネスわかったランド (経理)
在庫管理
作業改善と固定費低減による原価低減
プロセスを検討することでみえるムダもある
作業改善による変動費低減と固定費低減
量産段階で、在庫単価を下げるもう1つの方法は、「作業改善」です。作業改善は、加工費と経費の削減により在庫に集約される原価を低減させます。作業改善の方法はさまざまですが、方針として、ムダをなくして「非付加価値時間」を減らし、作業に関わる時間を可能なかぎり、製造行為そのものである「付加価値時間」に投入できるように改善します。
要は「ムダ取り」です。ムダ取りの方法はたくさんあります。動線を整理してムダな移動をしない、加工中に段取り準備をして段取り時間を削減する、部品搬送専任者をつくって作業者が部品を取りに行かずに作業に集中できるようにするなど、さまざまな観点で作業改善が行なわれます。
また、図表に示したECRSという考え方で、ムダをなくす指標として改善案を考えたりします。こうした方法は、IE(Industrial Engineering)として手法化されています。
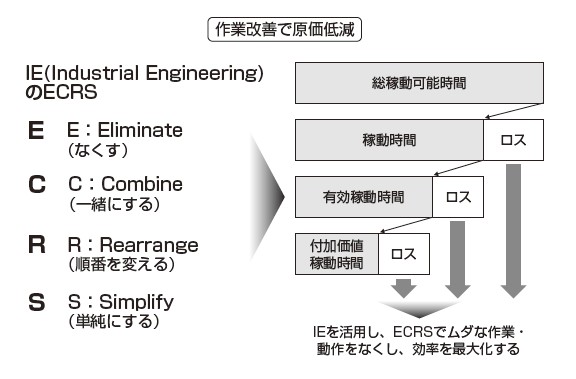
ムダ取り以外でも、「パフォーマンス向上」という方法で原価低減します。パフォーマンス向上とは、同じ時間を使って出来高を上げることです。1時間で100個の製造と1時間で200個の製造では、2倍パフォーマンスが上がっています。1個あたりに算入される作業費用は半分になっているわけですから、その分、原価が低減されているのです。
要は「ムダ取り」です。ムダ取りの方法はたくさんあります。動線を整理してムダな移動をしない、加工中に段取り準備をして段取り時間を削減する、部品搬送専任者をつくって作業者が部品を取りに行かずに作業に集中できるようにするなど、さまざまな観点で作業改善が行なわれます。
また、図表に示したECRSという考え方で、ムダをなくす指標として改善案を考えたりします。こうした方法は、IE(Industrial Engineering)として手法化されています。
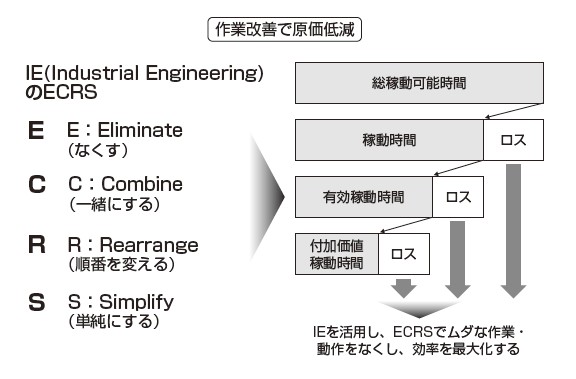
ムダ取り以外でも、「パフォーマンス向上」という方法で原価低減します。パフォーマンス向上とは、同じ時間を使って出来高を上げることです。1時間で100個の製造と1時間で200個の製造では、2倍パフォーマンスが上がっています。1個あたりに算入される作業費用は半分になっているわけですから、その分、原価が低減されているのです。
ABC(活動基準原価計算)の活用
ABC(Activity Based Costing:活動基準原価計算)は、会計の分野で登場した原価計算の1手法です。配賦基準をより現実に合わせて正しく設定していこうという考え方です。
まず、製造間接費を「コストプール」という原価の集計勘定に集めて、より正確に原価を配賦できる「コストドライバー(配賦基準)」を測定して配賦を行なう手法です。
簡易な配賦基準である人数や生産量などの「方便」ではなく、実際に原価に影響を及ぼす作業などの活動を特定し、それをコストドライバーとして設定することで正確な原価計算を行ない、より利益率の高い製品の選択や、優先的にコストダウンを行なう対象をみつけることを実現します。
たとえば、ある工場で、伝票処理作業にかかる人件費を製品出来高で配賦しているとします。しかし、よく調べると伝票処理作業がぼう大な品目とそうでない品目がありました。そうであれば、伝票処理作業に時間がかかる品目のほうが、コストがかかっているはずです。出来高では正確に配賦できず、原価計算が不正確になります。このようなケースでコストドライバーを伝票枚数ととらえ、伝票枚数を減らす改善活動を行なうのです。
ABCによって、活動(コストドライバー)の分析結果から、原価を発生させるプロセスを明らかにし、プロセス改善が行なわれるようになりました。ABCからABM(Activity Based Management:活動基準原価管理)へと進化することでビジネス・プロセス・リエンジニアリングが進み、在庫の原価低減にも役立つのです。
まず、製造間接費を「コストプール」という原価の集計勘定に集めて、より正確に原価を配賦できる「コストドライバー(配賦基準)」を測定して配賦を行なう手法です。
簡易な配賦基準である人数や生産量などの「方便」ではなく、実際に原価に影響を及ぼす作業などの活動を特定し、それをコストドライバーとして設定することで正確な原価計算を行ない、より利益率の高い製品の選択や、優先的にコストダウンを行なう対象をみつけることを実現します。
たとえば、ある工場で、伝票処理作業にかかる人件費を製品出来高で配賦しているとします。しかし、よく調べると伝票処理作業がぼう大な品目とそうでない品目がありました。そうであれば、伝票処理作業に時間がかかる品目のほうが、コストがかかっているはずです。出来高では正確に配賦できず、原価計算が不正確になります。このようなケースでコストドライバーを伝票枚数ととらえ、伝票枚数を減らす改善活動を行なうのです。
ABCによって、活動(コストドライバー)の分析結果から、原価を発生させるプロセスを明らかにし、プロセス改善が行なわれるようになりました。ABCからABM(Activity Based Management:活動基準原価管理)へと進化することでビジネス・プロセス・リエンジニアリングが進み、在庫の原価低減にも役立つのです。
キーワード検索
タイトル検索および全文検索(タイトル+本文から検索)ができます。
検索対象範囲を選択して、キーワードを入力してください。